Dicas de separação de cápsulas para reduzir tempo e desperdício
Tem escutado alguma vez a frase de que menos é mais? Isto aplica não só para temas de desenho e arquitetura, mas também para áreas de manufatura em geral. Por exemplo, no processo de fabricação de cápsulas duras, os desafios da separação podem ser resolvidos em muitos casos, simplesmente com a redução da pressão do vácuo.
Desde Nossa equipe de serviço técnico, compartilhamos as seguintes práticas que lhe ajudarão a superar os problemas mais frequentes na separação das cápsulas, ao tempo que lhe permitirão reduzir o desperdício de material e o uso dos equipamentos:
- Aceder, revisar e controlar a pressão do vácuo na máquina de enchimento, em todo momento
- Cumprir com todos os requerimentos de vácuo do fabricante original
- Entender o funcionamento das cápsulas vazias
- Configurar e controlar continuamente as condições das máquinas
- Minimizar os efeitos das funções da máquina de enchimento para assegurar uma ótima operação geral
É possível separar o processo de enchimento das cápsulas em funções individuais da máquina para assegurar uma operação mais fluida e eficiente. Estas funções são: retificação, separação, enchimento, expulsão de cápsulas defeituosas, fechamento, expulsão e limpeza das ferramentas.
No primeiro passo, as cápsulas orientam-se na posição adequada e localizam-se na máquina, logo após vem a etapa de separação das cápsulas, onde aplica-se pressão de vácuo para separar a tampa do corpo. A separação considera-se exitosa, quando as tampas ficam localizadas na ferramenta superior e os corpos, se mantêm na ferramenta inferior, sem defeitos e antes de que a ferramenta avance até a estação de enchimento.
Uma separação defeituosa evidencia-se de múltiplas maneiras, mas a mais comum é quando as cápsulas não se separam e a máquina as expulsa. Não obstante, existem outros signos de problemas de separação como a perda de tampas ou corpos, a geração de furos, os defeitos nas pregas do corpo e outros. Estes problemas originam-se por uma errada configuração das funções de separação e geram diminuição da produtividade.
O indicador de vácuo e a válvula de alívio de pressão
Edwards Deming (engenheiro e assessor independente norte-americano) afirmou: “Não podes manejar o que não podes medir”. Isto é muito relevante para os processos de manufatura de cápsulas vazias, pois muitos dos problemas com os que se encontram os expertos em serviço técnico, estão relacionados o mal funcionamento da válvula de vácuo.
Carecer do correto funcionamento de dita válvula é como dirigir um automóvel na chuva com os para-brisas avariados. A visibilidade é mínima e a capacidade de reagir é limitada.
A maioria das válvulas industriais manejam um indicador de medição por barras ou polegadas de mercúrio e com o passo do tempo, os indicadores podem se ver obstruídos com partículas de produto ou simplesmente avariar-se. Quando isto sucede, devem substituir-se imediatamente, já que a sua função é permitir a configuração e medição adequada dos níveis de vácuo.
Uma prática comum, mas errada é operar o equipamento com toda a pressão de vácuo disponível, o que implica em problemas como a dificuldade de notar o surgimento de furos ou a que as tampas não se acoplem corretamente nos orifícios das ferramentas, o que faz que estas caiam sobre a tabela do equipamento.
Para ajustar adequadamente o vácuo numa linha de produção, os operadores devem reduzir a pressão de vácuo (usando uma válvula de alívio de pressão) até que não se apresentarm mais casos de falta de separação.
Logo após, o operador deve incrementar vagarosamente a pressão de vácuo até que consiga a separação completa, monitorando o indicador para se assegurar de não aplicar um excesso de vácuo nas cápsulas, que possa gerar danos.
Adicional a previr defeitos de produção, o uso de um indicador que funciona corretamente ajuda ao operador a solucionar situações indesejadas com maior confiança e rapidez. É comum ver operários medir ditas situações de maneira subjetiva como através da sensação de sucção das mangueiras ou pelo som que gera o fluxo do vácuo. Isto evita-se, com o correto funcionamento do indicador de pressão.
Cumprir todos os requerimentos de vácuo do fabricante original
Muitos problemas de serviço técnico originam-se por não contar com o nível de vácuo recomendado pelo fabricante da máquina. Em muitos casos, a bomba de vácuo não está configurada apropriadamente de acordo com o tipo de máquina.
Um excesso de vácuo pode gerar que as cápsulas não se acoplem bem na ferramenta; o qual também pode ocorrer quando a bomba está muito distanciada da máquina de enchimento, pois entre mais espaço exista entre a bomba e a máquina, menor será o nível de vácuo.
Ao medir o nível de vácuo no indicador da máquina de enchimento (não da bomba) deveria obter o nível recomendado pelo manual do fabricante do equipamento. Este nível pode diferir de uma marca para outra, devido às diferenças de desenho e capacidade.
A força necessária para abrir as cápsulas (denominada força de pre-bloqueio) diferirá de um fornecedor de cápsula para outro, pelas diferenças no desenho dos pinos. Outras flutuações adicionais na força de pre-bloqueio podem se apresentar com base nas variações dos processos de manufatura. Para prever estas diferenças, avalie os seus processos e se assegure de poder ajustar oportunamente o vácuo disponível tanto para o máximo quanto para o mínimo nível recomendado pelo fabricante do equipamento.
Tem que evitar as variações excessivas dentro do mesmo lote ou caixa de cápsulas, já que isto gera que os operadores tenham que ajustar constantemente entre cápsulas frouxas e apertadas que correm simultaneamente, o que ao final implica desperdício de cápsulas e material.
Expectativas do uso das cápsulas vazias
As cápsulas vazias datam de faz mais de 100 anos e, mesmo de que se têm realizado melhoras importantes no seu desenho, a estrutura principal segue sendo a mesma. As cápsulas antigas que sobrevivem ao nosso tempo mostram que as predecessoras das cápsulas modernas não contavam com cunhas de fechamento que ajudarão a garantir que a cápsula se mantivera fechada, nem tampouco cunhas de ventilação. Estas características são padrão na atualidade e obedecem a melhoras que favorecem o rendimento e o estocagem das cápsulas.
As expectativas atuais sobre o desempenho das cápsulas vazias estão mais altas do que nunca. Os equipamentos modernos conseguem encapsular pós, pellets, tabletes e líquidos a velocidades de 400.000 cápsulas por hora, e considera-se que o tempo disponível para a separação apropriada das cápsulas, é de tão só segundos, evidencia-se que tanto os equipamentos quanto as cápsulas modernas devem ter um desempenho superior.
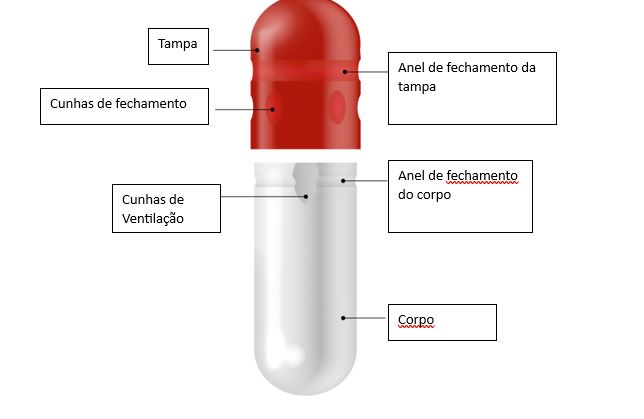
As cápsulas vazias chegam à máquina de enchimento numa posição de pre-fechamento. As cunhas de fechamento são umas fendas pequenas de forma oval, localizadas no perímetro da tampa da cápsula, que sobressaem para o interior da tampa e geram um baixo nível de fricção da tampa com o corpo, o que mantém estas partes unidas, até que a cápsula é carregada e assentada na máquina de enchimento.
A força necessária para fazer o pre-fechamento deve ser firme, mas pela sua vez o suficientemente ligeira como para poder abrir a cápsula com os dedos. As cápsulas vazias que têm um pre-fechamento ligeiro permitem o uso de vácuo ao nível mínimo. É importante ter acesso a ajustes adicionais durante este processo, já que os equipamentos e sistemas podem acumular produto durante a linha de produção, o que pode afetar a separação.
Também é importante ter em conta que o tamanho correto da cápsula favorece a separação adequada das suas partes. Se o diâmetro da tampa é muito largo, por exemplo, pode gerar constrição quando ingresse na parte superior do equipamento, o que pela sua vez aperta o corpo, impedindo que este se separe corretamente da tampa. É como se pusesse um cinto muito apertado ao redor da tampa da cápsula, o que obviamente impediria que o corpo se separe desta.
Muito pelo contrário, se o corpo da cápsula é muito largo, põe uma pressão excessiva no interior da parede da tampa, causando fricção e impedindo a separação das partes.
A estocagem e o manejo das cápsulas também podem afetar a separação. Os fornecedores de cápsulas vazias devem fornecer a listagem de condições apropriadas de temperatura e umidade de cada caixa de cápsulas produzidas.
Uma variação aceitável de temperatura para cápsulas de gelatina é de 59 a 77 graus Fahrenheit ou de 15 a 25 graus Celsius. Para cápsulas HPMC (Hidroxipropilmetilcelulose), a variação adequada é de 59 a 86 graus Fahrenheit, ou de 15 a 30 graus Celsius.
Ez termos de temperatura, os problemas mais comuns são: estocar as cápsulas em depósitos que não contêm com a temperatura ambiente adequada ou deixar as cápsulas nas canouras das máquinas por tempos de inatividade demasiado prolongados. Se o seu equipamento vai ficar parado por mais de um par de horas, é preciso remover as cápsulas vazias e reposicioná-las num contêiner selado.
No espectro oposto dos problemas de separação, estão as cápsulas que se abrem antes de que ingressem na máquina de enchimento, conhecidas como peças frouxas. Estas partes usualmente são rejeitadas no processo de retificação, mas também podem ocasionar que os carregadores se enguiçam, o que obriga aos operários a deter o processo para limpá-los.
A baixa umidade também pode aumentar a quantidade de peças frouxas, devido ao incremento da eletricidade estática. As cápsulas vazias desempenham-se melhor quando a umidade na máquina de enchimento é superior a 35%.
Outros fatores que contribuem à geração de peças frouxas, é aplicar uma força de pre-fechamento muito fraca, manejar as cápsulas de forma brusca ou usar processos de transferência de cápsulas pneumáticos, com uma turbulência ou força excessiva.
Configuração e revisão de condições ótimas da máquina de enchimento
Quando as cápsulas passam do processo de retificação ao de separação, os dedos do carregador as empurram de arriba para abaixo, desde o bloco de retificação para a ferramenta. Antes de chegar ali, as cápsulas devem estar completamente verticais e posicionadas exatamente acima dos orifícios. Se as cápsulas entrarem em contato com o segmento superior antes de que ingressem nos furos, se fecharão e não poderão ser separadas. Ajustar os dedos do carregador horizontal de maneira frequente, resolve este problema.
Os segmentos superiores e inferiores que recebem as cápsulas do processo de retificação também devem estar alinhados e limpos para permitir que as cápsulas ingressem facilmente nos orifícios, se separando.
A distância entre as paredes da cápsula e o equipamento é de apenas uma milésima de polegada, pelo que qualquer discrepância causada por um errado alinhamento, por orifícios sujos ou por danos nas paredes da ferramenta, podem afetar o processo de separação.
Os segmentos superiores e inferiores deveriam estar sempre alinhados sem dificuldade nem partes frouxas. Para equipamentos que usam caixa de engrenagens para o movimento de torreta, é imprescindível realizar manutenções técnicas periódicas de alinhamento da ferramenta para assegurar que a posição dos segmentos esteja centrada a respeito às estações auxiliares durante o processo de traslado da torreta, especialmente desde a estação de fechamento da cápsula até a estação de separação.
A caixa de engrenagens pode se desviar do centro a respeito ao orifício da mesa, amiúde como resultado de um choque da máquina. Para revisar isto, é preciso alinhar os segmentos na estação de fechamento e ajustá-los no seu lugar, logo após deve-se passar a máquina por cada estação sucessiva até a estação de separação, se detendo em cada posição para se assegurar de que os pinos de alinhamento caiam no seu lugar.
Várias máquinas comerciais usam pinos de separação, o que ajuda a controlar a descida das partes da cápsula na ferramenta. A distância correta dos pinos é de 1/16 de polegada a 1/8 de polegada (1.5mm a 3mm), desde a ponta do pino até o domo do corpo das cápsulas, quando os pinos estão na sua posição mais alta. O espaço reduzido entre o pino e o corpo da cápsula ajudam a que a cápsula se libere da posição de pre-fechamento durante o processo de separação.
Como ajustar corretamente a altura dos pinos?
O primeiro passo é remover o segmento inferior da máquina de enchimento, deixando o segmento superior no seu lugar. Logo após deve-se carregar as cápsulas manualmente no segmento superior no estado original de pre-fechamento. Logo após deve-se posicionar o segmento sobre a estação de separação e rotar a máquina de maneira manual até que os pinos de separação estejam no ponto mais alto. Finalmente, com o segmento inferior removido, deve-se revisar e ajustar até obter a separação recomendada.
Este ajuste deve-se realizar no momento de cambiar os tamanhos das cápsulas e também quando mude o fornecedor de cápsulas vazias.
Estação de limpeza
As estações de limpeza têm evoluído amplamente ao longo dos anos. As versões mais antigas eram simples campanas de colheita de pó, pelas que os segmentos passavam rapidamente. Em contraste, as versões modernas incluem múltiplas configurações como por exemplo, o fato de que alguns pinos de limpeza são ocos e têm orifícios que proporcionam uma rajada de ar comprimido nos orifícios das ferramentas.
As máquinas também se podem programar para que gerem uma rajada de ar em cada movimento de repasse ou em intervalos de tempo programáveis. Em casos onde o material de recheio é difícil de manejar ou cola-se à ferramenta, se podem utilizar escovas de limpeza descartáveis que se estendem da ferramenta inferior à superior.
É preciso se assegurar de contar com um coletor de pó adequado para remover o pó frouxo durante a etapa de limpeza. Para a tecnologia de recheio líquido, vários equipamentos contam com sensores que detectam cápsulas faltantes e indicam à máquina para não liberar o líquido, o qual mantém limpa a ferramenta.
Finalmente, é recomendável se assegurar que a retificação das cápsulas esteja configurada adequadamente para permitir que estas separem-se de maneira uniforme, antes de introduzir o material de recheio. Também pode fazer pequenos ajustes ao vácuo proporcionado na linha de produção pois os componentes tendem a se encher de material de recheio. Se tem problemas com a separação das cápsulas ou com qualquer outra parte do processo de enchimento, se comunique com a equipe de serviço técnico do seu fornecedor de cápsulas vazias.